What We Can Customize for Your Composite Bags?
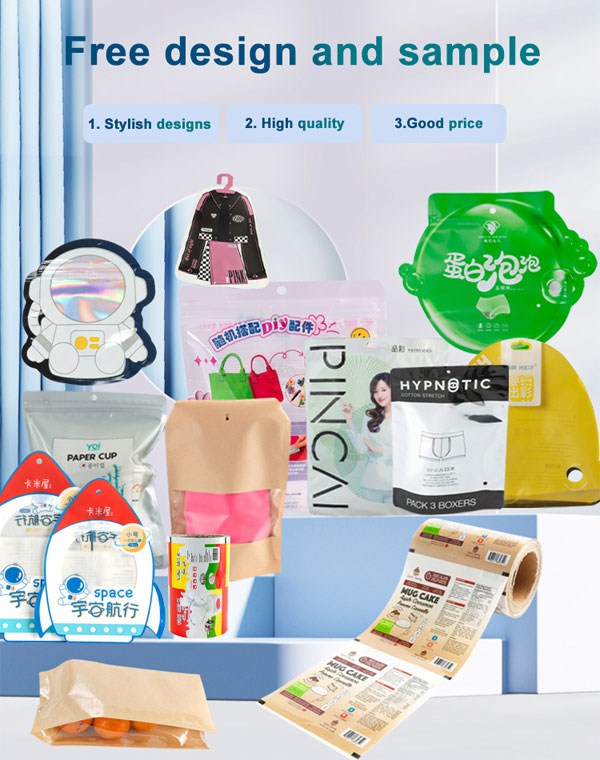
- Customized or recommended
- 3/4/8-side seal
- Stand up
- Flat-bottom
- Side gusset
- Zipper Top
- Heat Seal
- Tin-tie
- CMYK or Pantone
- PET + PE
- PA + PE/RCPP
- PET + VEMPET + PE/CPP
- BOPP+ PE/ CPP / VMCPP
- MATT BOPP + VMPET/PET + PE
- MATT BOPP +PAPER + PE /CPP
- PET +AL+ PE/ RCPP
- PET +AL + PA + PE/RCPP
- Lamination
- Printing
- Embossing / Debossing
- Varnishing
- Foil Stamping
- Matte Coating
Custom Bag Type Options
We provide a template, which help you translate your specific needs into a functional and visually appealing design.
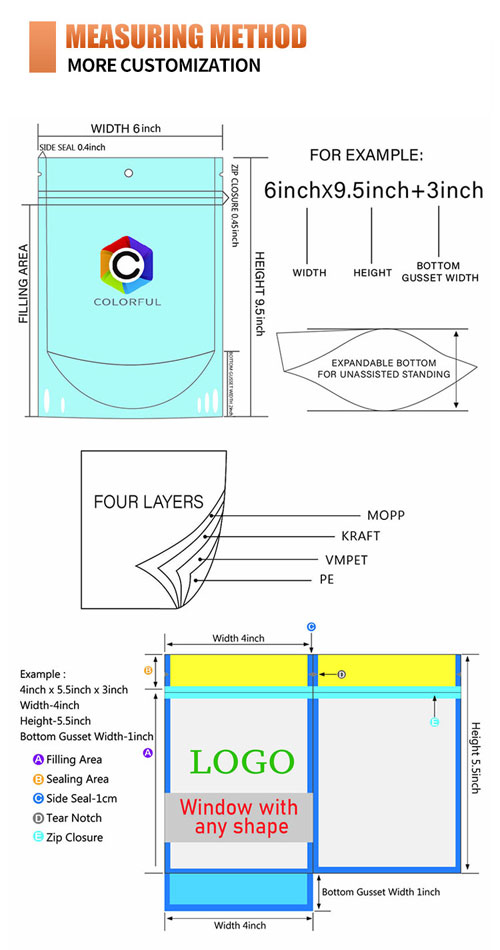
Common-style composite plastic bags are usually pre-designed, cost-effective and come in standard sizes and shapes. But they might lack uniqueness and customization.
Here are some common composite bag styles:
- 3/4/8-side seal bag
- Back seal bag
- Stand up pouch
- Zipper bag
- Curl-up film
- Flat-bottom bag
- Side gusset bag
- Heterotypic bag
- Three-dimensional side bag
We can help you customize composite bags by combining the various styles mentioned above. For example, a popular option is a stand-up pouch with side gussets, which combines the stability of a stand-up bag with the extra capacity provided by gussets.
Additionally, consider other design elements like the material composition, closure mechanisms (zipper, tin-tie, etc.), printing and branding options, and any special features required for your product.
Bag Sealing & Handle
Provide convenience and security for various packaging and carrying purposes.
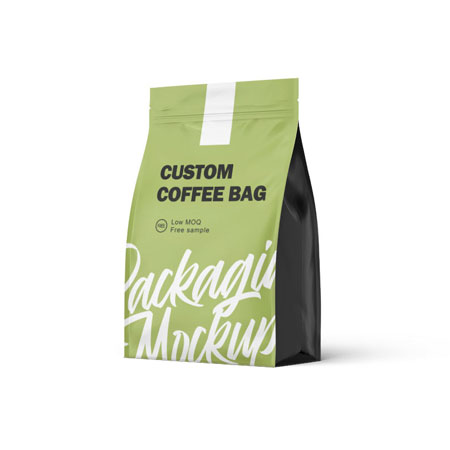
Zipper Top
The bags are equipped with a resealable zipper at the top, allowing consumers to easily open and close the bag frequently while maintaining the freshness of the product inside.
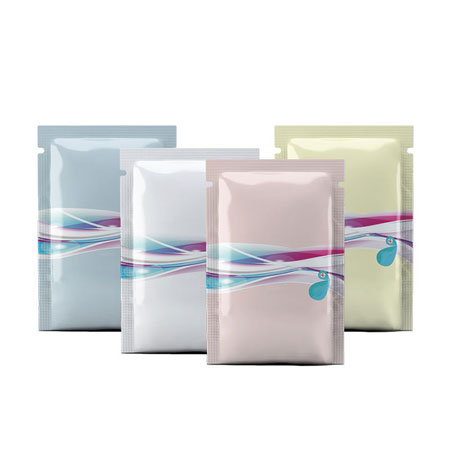
Heat Seal
The heat sealing process involves the application of heat and pressure to the bag's edges to melt and fuse the layers of plastic together. This creates a strong bond that prevents any leakage.
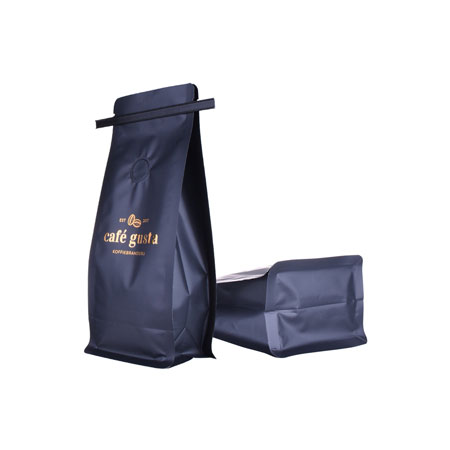
Tin-tie
The tin-tie closure is a small, flat piece of tin, which is adhered to the top of the bag's opening. By folding down the top of the bag and twisting the tin-tie, the bag can be securely closed.
Bag Surface Finishing
The purpose of surface finishing is to improve the bag's appearance, functionality, and overall user experience.
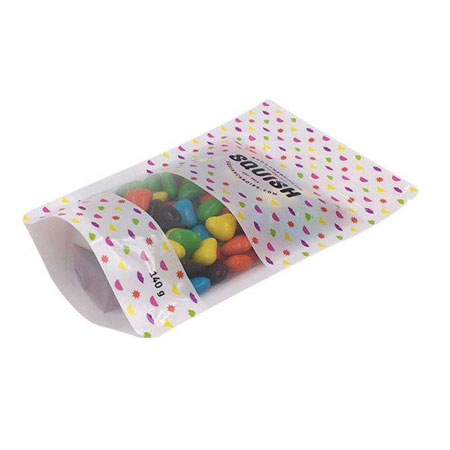
Lamination
Lamination involves bonding a thin layer of plastic film onto the surface of the bag. This process can improve the bag's strength, water resistance, and overall durability.
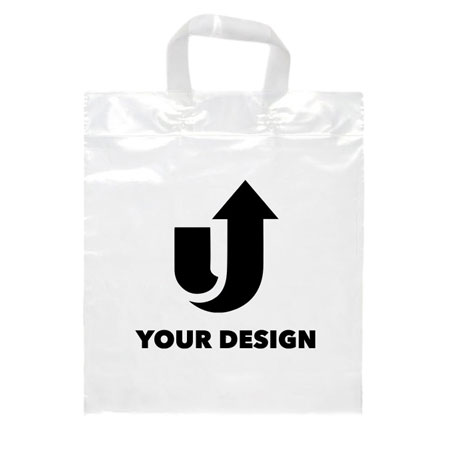
Printing
Printing is one of the most common surface finishing methods for plastic bags. It allows to add branding, logos, artwork, and information on the bag's surface.
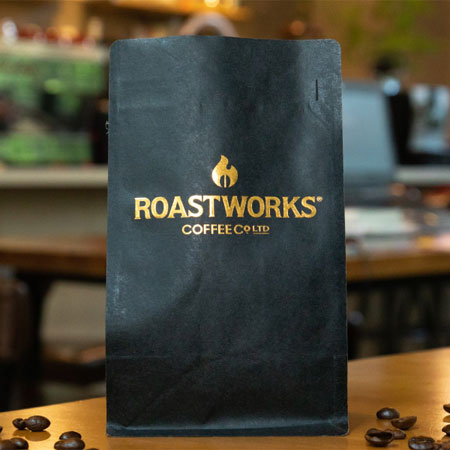
Embossing/Debossing
Embossing creates a raised pattern on the surface of the bag, while debossing creates a depressed pattern. These processes add texture and a tactile element to the bag.
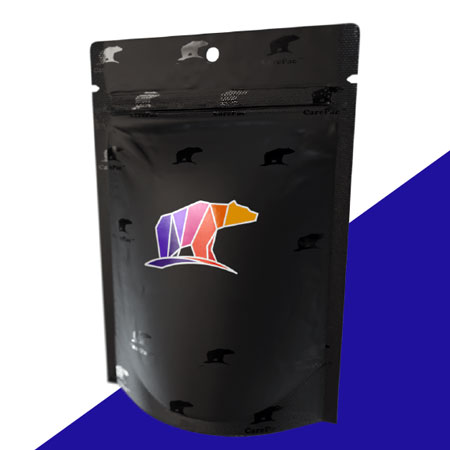
Varnishing
Varnishing is the process of applying a clear protective coating to the bag's surface. It can enhance the bag's durability and protect the printing or graphics from wear and tear.
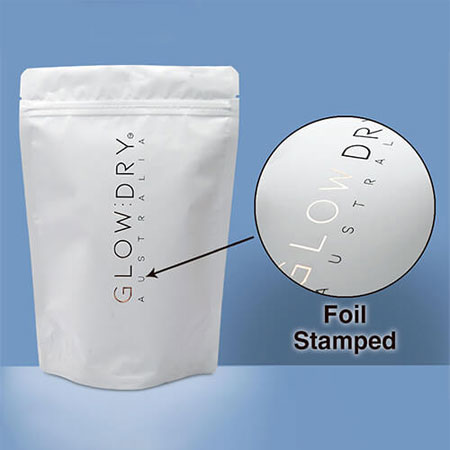
Foil Stamping
Foil stamping involves using heat and pressure to apply metallic foils onto the plastic bag's surface, adding a premium reflective look to the bag.
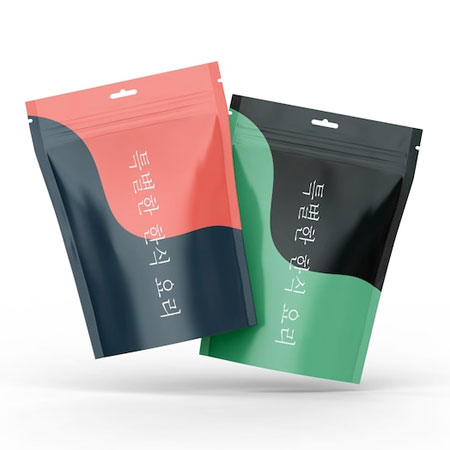
Matte/Glossy Coating
Applying matte/glossy coatings to the bag's surface can give it a specific texture and non-shiny, subdued or shiny and reflective appearance.